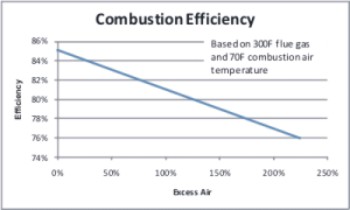
Maintenance Is Important
Remember taking your car in for tune-ups, messing around with the carburetor and so forth? I didn’t think so; neither do I.
Boilers, like cars, are slowly transitioning from mechanically-controlled combustion components to electronic controls. I don’t know the percentage of each, but believe me when I tell you there are an awful lot of mechanically-controlled boiler burners in operation today. Now the important question, is your boiler operating at its peak efficiency? If it hasn’t been tuned up recently, then odds are it’s not. Here are a couple of boiler controls that can be easily tuned up.
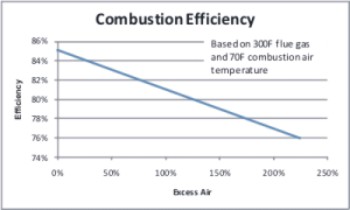
The Air to Fuel Ratio
The air to fuel ratio used for combustion has a major effect on the efficiency of the boiler. If the mixture is too rich (e.g. there is insufficient combustion air for the fuel flow) then some of the unburned fuel will leave the boiler through the exhaust flue. If the mixture is too lean (e.g. too much combustion air) then excessive air will leave via the flue, carrying heat with it. The air to fuel ratio is typically kept slightly lean to ensure that complete combustion occurs. The ideal range to operate at is about ten to twenty percent excess air. Typically, excess air runs at 20-50% or even more.
The air to fuel ratio is controlled with either a jackshaft (cam) mechanical system or an electronic linkageless control system. A boiler professional can “tune up” the boiler to optimize the air to fuel ratio on either type of control system. One benefit of the linkageless control system is that the air to fuel ratio can be optimized across the entire range of firing rates, as opposed to a jackshaft system which can only be optimized at a couple of firing rates.
The Control Band
Another thing to check when evaluating your boilers is the control band. The control band is essentially the pressures (for steam) or temperatures (for hot water) at which the boiler will kick on and turn off. Setting this band too narrow will cause excessive cycling of the boiler, which is not a good thing.
Boilers have to go through a pre-purge cycle before firing can commence, and then a post-purge cycle once the burner has completed firing. During both of these purge cycles, the air inside the boiler is purged and replaced with fresh air. The purpose of this is to remove any combustible gas mixtures that may still be in the boiler. Relatively cool boiler room air flushes the boiler and thus the boiler is cooled down. The energy removed from the combustible gases and the boiler shell via purging is energy lost. If cycling is frequent, these losses can add up quickly.
For example, if you have a low pressure steam boiler operating with a control band from 8-10 psi, consider expanding the band to 6-12 psi. This will reduce boiler cycling. Note that a narrow control band is not the only cause of frequent cycling. An oversized boiler can also be the reason that frequent cycling occurs. For more information on oversized boilers, please see our previous Energy Brief titled “Boiler Misconceptions.”
Don’t Forget the Tune-Ups!
Remember to periodically “tune-up” the items mentioned above. It will not only improve the efficiency of your boiler, but could lead to a longer life for your boiler as well.