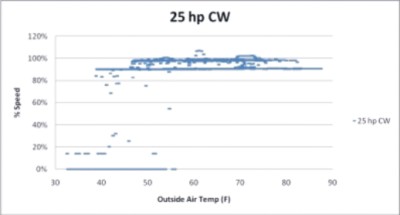
Lately, the majority of the work I have been doing is measurement and verification work for utility program evaluations. This work involves numerous onsite visits to verify that the programs are saving what they are claiming. In the process of doing these site visits, I have seen some interesting things, and in particular for this brief I want to discuss findings with freshly installed variable frequency drives or VFDs. To review how to save energy with VFDs, see “Putting Out Cash Fires with VFDs”. To see how to not save energy with VFDs, keep reading.
VFDs Only Work When Connected to Motors
That’s right. Evaluators and program managers frown upon VFDs hanging on a wall with conductors visibly connected to nothing.
VFDs are great… if you program them
Surprisingly enough, many VFDs don’t save energy. I find them installed and running at 100% speed / 60 Hertz. In fact, since VFDs are not 100% efficient, they use even more energy in this condition than using the motor alone. I have seen far too many new VFDs running at 100% speed.
Along the same lines as not programming the VFD with new controls is not disabling the old controls. I reviewed a project for a major retail store where they installed VFDs on the refrigeration condenser fans. Unfortunately, no one disabled their old controls so before the VFDs could modulate the speed of the fans down, the existing controls would shut fans down in sequence forcing the VFDs to stay at 100% speed. This should have been a great project but all that was accomplished was added inefficiencies to the system due to the unavoidable and typically minor by comparison VFD losses.
VFD is more than a fancy word for soft starts
One of the first questions I ask the customer is why he or she installed the VFD. I like to do this so I know what the primary goal was for completing the project. Installing a VFD to perform as a soft start so you don’t blow out your flexible coupling when the second chilled water pump kicks on typically does not lead to any drastic energy savings. To be fair, the customer did change the speed to 0, 90 or 100% speed based on water temperature but this method leaves a large chunk of the energy savings on the table. Continuously modulating motor speed to maintain system pressure or by valve positions will give you the maximum savings possible while in this case, avoiding the possibility of starving cooling coils of chilled water. In the chart, it is apparent that the motor is modulating between two different speeds and off. The points between are just times when the loggers caught the motor transferring between the two.
Summary
VFDs are capable of great energy savings if you take the time to program and optimize a good control scheme. You should be continuously modulating the speed to meet the current conditions not setting a fixed speed that works for all conditions. This is even more important if you are pursuing a rebate as many utilities require automatic controls to qualify and setting a fixed speed is not automatic.