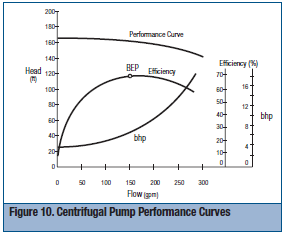
Oversized pumps seem to be a common epidemic throughout pumping systems, whether in a production plant or an HVAC system. Not only do oversized pumps increase initial costs, they increase both energy and maintenance operating costs, increasing Life Cycle Costs (LCC) for the entire system.
Call to Order
A primary reason for improper pump selection is lack of system standards beginning at the design phase. Continued use of past design approaches, as well as time and budget constraints, cause conservative engineering. This often results in the selection of a pump that is “one size up”, adding safety margins for uncertainties and/or anticipated future growth. Other cost cutting measures include installing the spare pump from storage to reduce project capital costs. Additionally, limited project planning or untimely failures lead to installing the “only” pump available which does not effectively match the system. Or the pump is replaced with the same size without consideration of whether the system has changed operating conditions or if the original pump was oversized.
Reporting for Duty Point
Pump curves provide a picture of the operating characteristics of the pump. Impeller diameter and rotational speed can change the shape of the pump curve. A system curve illustrates the required head pressure for the flow rate desired. During the pump selection process, the two curves are overlaid with their intersection being the point of operation, often called the Duty Point.
A properly sized pump will have a Duty Point as near as possible to the pump’s best efficiency point (BEP). Normal operating ranges for pump systems is within 65 to 85 percent of the BEP. Pumps operating well below the BEP consume excess energy, which has to go somewhere. Typically, this excess energy is transferred into heat, vibration, and noise, which increases utility costs, maintenance, and potentially premature equipment replacement.
Shape Up
In order to optimize a pumping system, it is important to investigate for signs of improperly sized pumps. Pumping systems with one or more symptoms would be ideal for further assessment for optimization. Such symptoms include highly throttled control valves, excess by-pass or recirculation lines, frequent pump on/off cycling or a change in the system operation without modification.
Replacing an oversized pump is not the only option when trying to optimize the system. Trimming the impeller diameter can reduce the energy consumed and bring pump operation closer to the BEP. In appropriate applications, a variable frequency drive can be an effective way to increase the efficiency of the system.
An optimized pump system goes beyond just an efficient pump and motor. It is important to look at the entire system, and installing properly sized equipment is a step in the right direction.