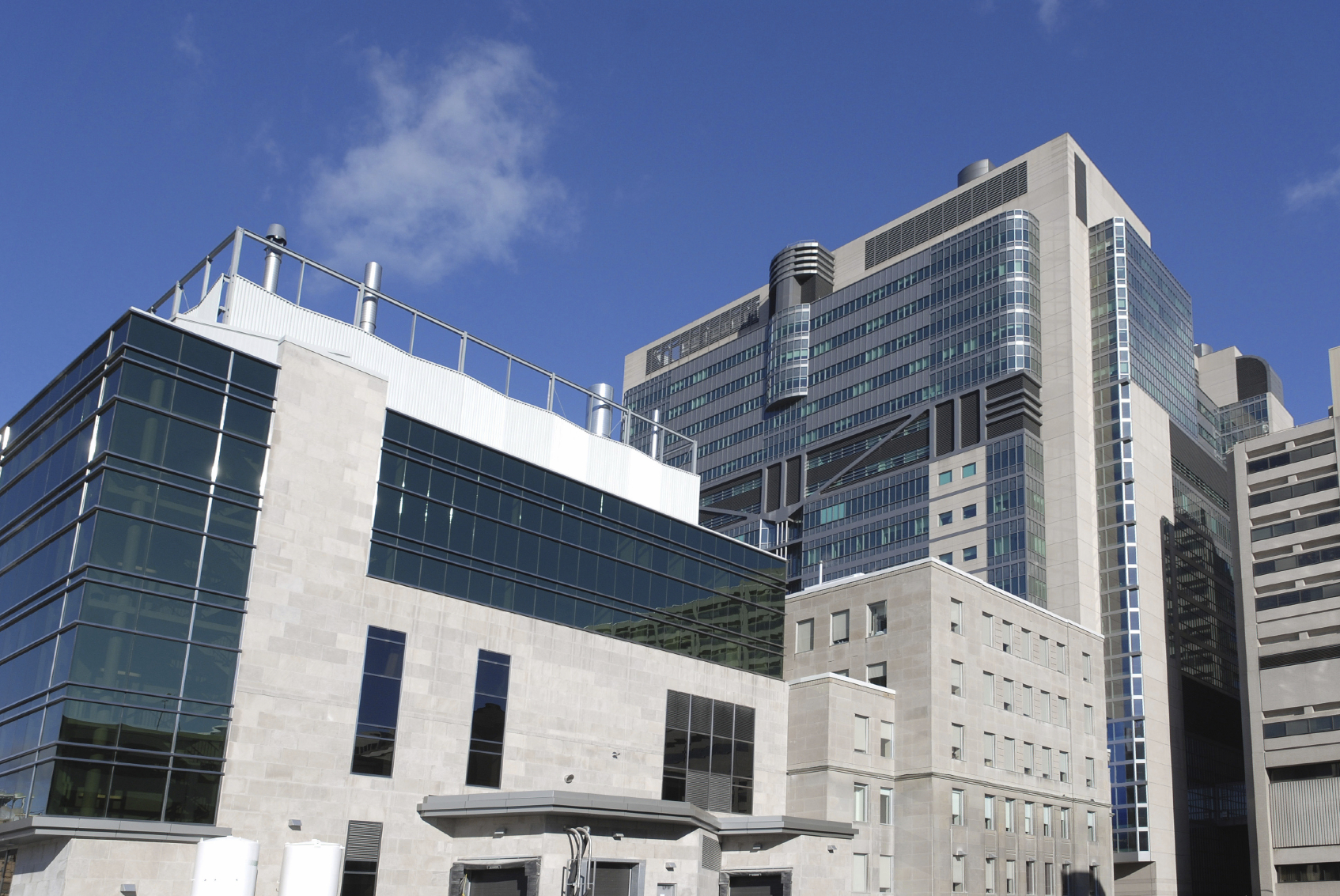
Changes in the production rate at an industrial facility can be a big stumbling block for energy efficiency projects. Program implementers and evaluators need to consider the operation of the equipment related to the project, but also what production changes may be taking place at the facility. This is not as simple as it may seem!
When examining projects for industrial or manufacturing facilities, program implementers need to have clear guidelines for handling changing production levels. The guidelines should specify key production scenarios, how to handle baselines, and how to normalize the savings to the appropriate production level. Of course, the guidelines should also be discussed with the program evaluator ahead time to avoid surprises in the future.
Equivalent production levels
One key characteristic of well analyzed projects is that equivalent production levels are used on both sides (before and after the project) of the analysis. The easy situation is similar production levels before and after the completion of a project. Unfortunately, this rarely happens. Customer production schedules and rates don’t revolve around efficiency programs. Program implementers have to be little flexible but consistent to accommodate production schedule and rate changes.
If production has decreased since a project, analysts need to know if it’s transient. A temporary dip in production should be ignored. Transient production decreases can be accounted for in the energy analysis by using the pre-project implementation production data as the common denominator.
The opposite is true when there is a significant production increase after a project. But there are more nuances in these situations. Production increases that could have been met by the old equipment are straightforward. The new production level is appropriate to use in the baseline and energy efficient cases when calculating savings. But estimating savings in cases where production levels couldn’t be met by the old equipment require a different approach. The appropriate baseline in these cases is “standard practice” equipment that is large enough to meet the new, increased production levels. Such a baseline can produce dramatically different results.
Similar processes
Keep a close eye out for facilities that serve several different functions. One example is a foundry that also completes machining work. This facility goes through cycles where casting is the primary production mechanism and other periods when machining is the primary energy load. The key is to make sure that energy consumption for the pre and post cases include similar production mixes. If data collection during similar methods isn’t possible, make sure enough data is collected so the analysis can be properly normalized to consistent production mixes.
Check with your evaluator
There are always exceptions and outliers when dealing with industrial facilities. One of the best resources available to programs are their current or previous program evaluators. Evaluators can provide project specific guidance, opinions, and risk identification. Many evaluators work in multiple jurisdictions throughout the country and can provide valuable insights from previous project experience.