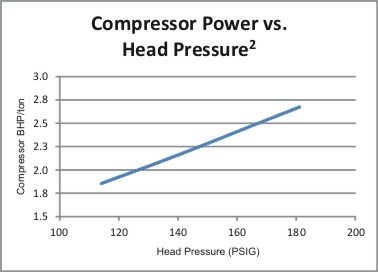
A Big Part of the Budget
Energy costs represent a significant expense for facilities that operate industrial refrigeration systems. For refrigerated warehouses in particular, it is estimated that utility costs can be as high as 17% of revenue1. One key way to cut these expenses is to optimize energy consumption of refrigeration systems.
Keep Optimization in Mind from the Beginning
Despite the high operational costs and energy use, refrigeration systems historically have been designed to meet the system load at the lowest up-front capital costs. In addition, systems are often expanded to meet production needs with energy considerations being a low priority. The good news is that significant savings can be achieved by incorporating efficient technologies during system design.
Floating Pressure
One of the most practical energy conservation technologies to implement is floating control of condenser head pressure. While this strategy is becoming more common with new system design, it can also be done practically as a retrofit. Standard design systems control head pressure to a fixed design condensing temperature, which is high enough to meet the maximum load. Floating head pressure controls allow for the condenser temperature set point to be reduced when ambient conditions are cooler. The set point reduction is made possible by the increased cooling capacity of the condenser at such conditions, meaning that the condensing temperature can be reduced while achieving the same amount of cooling. See the chart to the left.
Some additional advantages to this control strategy include a decrease in the compressor oil cooling load as well as increased compressor life. The trade-off is an increase in condenser fan energy; however, this disadvantage can be mitigated to a degree with an oversized condenser.
Condenser Considerations
While only practical for new system design, an oversized condenser is often used in conjunction with floating head pressure controls. A larger condenser enables a lower condensing temperature, which reduces compressor work. Although it requires increased front-end cost in the form of larger equipment, typically the energy saving benefits outweigh the costs.
It should be noted that the degree which the condensing temperature can “float” will be determined by the ambient conditions. Head pressure reduction is also limited by other system components such as the cooling coil control valve.
Conclusion
While these strategies are just two of many efficient design concepts, energy saving rates of over 20% can be expected in many systems3.
1 2010 IARW Productivity and Benchmarking Report (http://www.gcca.org/cold-facts/energy-savings-in-refrigerated-warehouses.html)
2 Data taken from a commercially available rotary screw compressor with a suction temperature of -22oF with R-717 refrigerant.
3 Average Savings Technology Report Industrial refrigeration and chilled glycol and water applications, Office of Environment Heritage Report (P12)