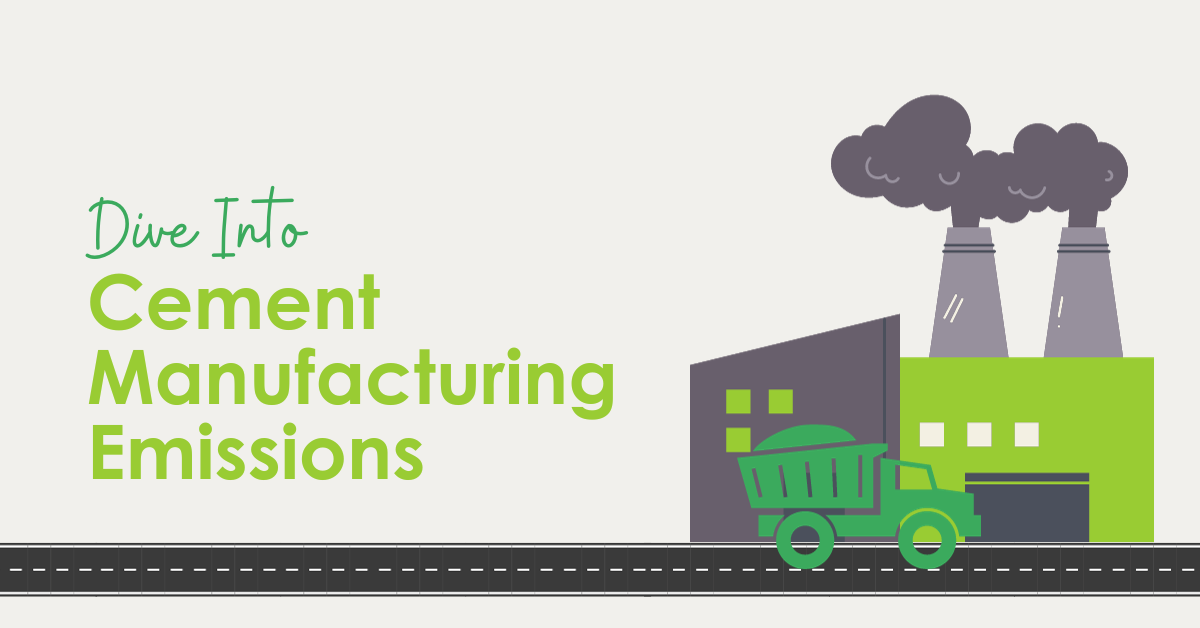
Over the years, I’ve seen numerous mentions of decarbonizing concrete or cement. Random articles describing the need and means to decarbonize cement include this McKinsey article, this DOE post, and this Canary Media article. Those don’t cut it for me. I set out to explore cement making and why it is so carbon-intensive.
But first, some terminology review is advised to differentiate cement from concrete. Growing up, in college, and even post-college, we used the term cement synonymously with concrete. E.g., “cement hands” to describe a guy who couldn’t catch a basketball or football or “cement head” to tell civil engineers. Each of those uses conjured blocks of concrete in my mind, not the powder that is cement, the key ingredient in concrete.
Cement, predominately Portland cement, is the fine-powdery ingredient that, when mixed with water, sand/gravel, aka aggregate, binds up and cures to form concrete. Portland cement is named after the Isle of Portland, England, not Portland, Oregon, or Maine. It was first patented in 1824.
The ambition to experiment with wild ideas in the days of yore, 200 years ago when Portland cement was patented, amazes me. Think about it for a minute. These folks probably hammered, pummeled, ground limestone and sand into powder, mixed it with water, and failed. “Shit, that didn’t work.” Maybe if we heat it to 2700 degrees Fahrenheit for a while, that would give it binding properties?? Let’s try that! It reminds me of Tom, the seasoned trapper man on History Channel’s Mountain Men. In one episode, he boiled coyote brains to smear on the pelts so they wouldn’t shrink and crack. Wow! I bet they didn’t get that right on the first try.
Portland Cement Carbon Impacts
According to Carbon Brief, cement production for concrete accounts for 8% of total global CO2 emissions. Carbon Brief says that 8% is more emissions than any country except China and the United States, and of course, China’s cement and CO2 emissions tower over every other country by a jaw-dropping margin.
Cement-Making Process from Mine to Bag
The cement-making process, from quarry to powdery cement for delivery to bagging operations or ready-mix concrete plants, is shown in the line diagram below.
Encyclopedia Britannica provides a more illustrative diagram to help visualize the process.
Raw materials, including limestone, a major ingredient, are crushed and pummeled into powder for feeding into the kiln. Years ago, we analyzed a custom rebate application for better mill media in the limestone “flour” manufacturing process. It featured iron balls in a rotating drum to pummel the limestone from rough ground limestone to fine ground limestone.
There are billions of photos of cement clinker, but I need to guess a little as to what the feedstock into the kiln looks like. I believe the feedstock is as follows per Agico Cement.
You might be thinking, wow, this process requires massive amounts of diesel fuel for excavators, earth movers, and trucks, plus electricity to grind the materials into powder. It is, but most of the energy consumption and carbon dioxide emissions are a result of the kiln, as shown below courtesy of Climate Brief. They say, “The production of Portland clinker, which acts as the binder, is a crucial step in making Portland cement. Limestone (CaCO3) is ‘calcinated’ at high temperatures in a cement kiln to produce lime (CaO), leading to the release of waste CO2. Overall, the following reaction occurs:”
Sources of carbon emitted in the cement manufacturing process are as follows: per Climate Brief – ninety percent are exhausted from the kiln!
The kiln fires to about 2700 degrees Fahrenheit, approximately the melting point of carbon steel. The shell of the kiln, shown below, is kept around 750F, using refractory (insulating bricks) inside the rotating kiln cylinder as it sinters the materials into cement clinker. These kilns produce cement at rates of 270 tonnes (270,000 kilograms), or about ten truckloads per hour.
Sintering fuses cement ingredients, without melting, into non-uniform balls of cement clinker with diameters of 0.1 to 1.0 inch. The clinker is cement in chunks. The clinker is ground into fine powder, making Portland cement ready for shipping.
Concrete Critical
Concrete has what I’d call non-critical uses, such as sidewalks and driveways, which carry minimal load, and no one dies when they fail. Other uses are much more critical: bridges, tall buildings, and parking ramps. I would classify roads as somewhere in between. Failure can be very costly and deadly.
Potential Replacements – Not Advised
According to Canary Media, some in the industry or around it (DOE) are considering decarbonizing concrete by reducing cement content and/or finding cement substitutes for concrete. Look out. Decarbonizing cement is not something I would force because force breaks things.
Even industries like road building still haven’t mastered the use of concrete. For instance, stretches of Interstate 90 from La Crosse, WI to Rochester, MN, were replaced with all-new concrete construction. A year or two later, in 2023, lanes were closed, and sections were being sawed out and replaced. Whoops. Was it the concrete? My guess is no, but teams of people make significant mistakes like that.
Carbon Capture?
Since CO2 emissions from this product/industry are so concentrated from one process, I would exhaust (pun alert) all efforts to capture carbon at the source before looking for catastrophic displacements of the critical material, Portland cement.