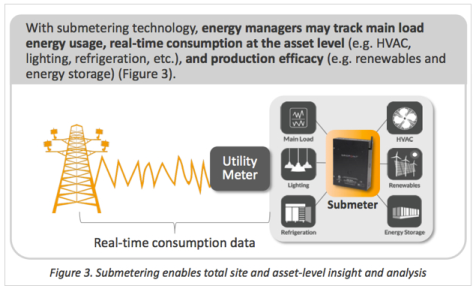
As the call for more cost effective products by the customer increases, industry is turning to new methods to help control costs, reduce waste, minimize downtime, and optimize processes and procedures. Conventional methods previously involved the collection of large amounts of data (often times by hand), analysis of that data using spreadsheets and calculations, and creation of reports to organize and summarize the results. This involved a lot of labor, and more than likely, a substantial time delay before actionable ideas could be implemented for improvement. The dataset was often so large it was practically impossible to use in real time.
Sub-metering, in conjunction with integrated software and analysis tools, is a newer method that is changing this approach and improving outcomes.
Sub-metering is the use of a meter, most often for electricity, natural gas, water, or some other commodity, that monitors usage on a portion of a distribution network, downstream of the utility, past a main meter. Sub-metering can be used in a variety of settings including residential, commercial, and industrial (focus of this brief).
Sub-metering is no longer a cost prohibitive solution. In fact, it’s becoming more and more cost effective, especially with the advent of less expensive, more compact electronics, wireless technologies, and integrated software. As a result, many end users are employing sub-metering with integrated software to collect and analyze more granular data about operations. This ultimately benefits the enterprise. Today, energy managers are using sub-metering to collect data at the asset level, or even the production level.
This allows the energy manager to use real time data available from sub-metering technologies to manage energy use as never before. Integrated solutions include smarter alarms, dynamic control of equipment and processes, proactive electrical demand response and peak shaving, and financial verification of production costs. All of these attributes can lead to an optimized process and improved, integrated sustainability.
Sometimes the largest hurdle to employing this technology (or anything new) can be the existing culture of the enterprise. The employees’ response will almost invariably be, “This is how the plant has always run”, or ”We’ve already employed all reasonable energy conservation efforts”, or ”We don’t have time for this”. As with any change, leadership is the key to success. Change has to start at the top.
It has been found and proven that with proper leadership, employees initially reluctant to change will find great value in sub-metering. Reviewing data and visualizing energy use across the production process, and eventually the entire plant, will awaken a number of possibilities for energy efficiency improvements. Allowing data driven decision-making empowers and energizes plant staff, helps senior leadership understand the bottom-line impact of proposed projects, and produces meaningful energy savings.
According to this case study by the US Department of Energy, the Nissan automobile manufacturing plant in Smyrna, Tennessee performed a sub-metering upgrade project in 2009. Upon completion of the project, the Nissan Energy Team Facilitator remarked, “The only disadvantage to sub-metering is that now we can’t imagine operating without it!” Ultimately, sub-metering with integrated software is a powerful and successful tool.