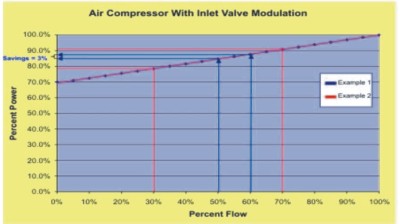
Oftentimes compressed air vendors and analysts equate each percent of compressed air saved to an equal percent of energy and dollars saved. This is rarely the case. In other words 30% compressed air savings will typically yield much less than 30% energy savings.
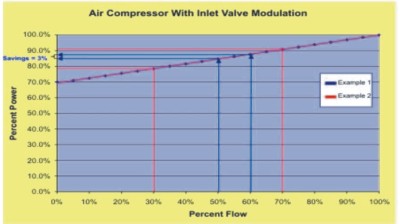
How Does it Work?
The graph shows the unloading characteristics of a typical air compressor with inlet valve modulation control. It can be seen that reducing compressed air flow by 10% will only reduce the power consumption by about 3%. For instance, if a compressor is loaded to 60% flow it is using 88% power. If that flow is reduced by 10%, it would still be using 85% power! This is illustrated in Example 1 of the graph.
Suppose compressed air demand is reduced a lot, from 70% to 30% of compressor capacity (Example 2). You might reduce compressor power only 12% of full load power. However, if the flow is reduced down to zero relying on other compressors that are running anyway, 91% of the full load power can be saved.
This holds true throughout the operating range of the compressor for this control type. In order to achieve a considerable amount of energy savings the compressed air demand must be reduced enough to shut a compressor off completely.
Other Types of Compressors
While the typical compressed air plant exhibits the above characteristics, the effects may not be as dramatic with compressors that unload efficiently. These compressors are worth the premium price but are not as common as those described above. At 60% flow, turn valve controls, for example, still require 70% power. The power consumption of a load-unload compressor at 60% flow is even less (~65%), and the power consumption of a variable speed compressor at 60% flow approaches 60% power. The different air compressor unloading methods will be discussed in depth in a future brief.
Getting There
There are numerous things that can be done to reduce compressed air demand. Fixing leaks is probably the easiest and most cost effective way to reduce the compressed air demand. For instance, eliminating a 1/8-inch compressed air leak and shutting a compressor off as a result can save over $2,000 per year. Improving end use controls is another effective way to reduce compressed air demand. The biggest compressed air savers can be eliminating inappropriate uses of compressed air. This will be discussed in a future brief.
In summary, the key to big time energy savings is shutting compressors off. In a typical compressor plant, if you can’t shut off compressors you are only getting the crumbs.